Guilda Masterbatch Flowboard Magazine
Figure 1: UV degraded roof of 22,000 Litre Dark Green Tank Most rotomoulders around the world have been accustomed to the phrase ‘long term outdoor performance’ to describe their UV stabilised raw materials. Many moulders have assumed their own moulded parts may have some claims to long term performance outdoors. However, the meaning of ‘long term’ is rather vague when it comes to performance under the sun. While there are some manufacturers who want to build in product failure, so they can replace products sooner rather than later, in the case of manufacturers of water and chemical tanks, the vast majority want their polymer, and moulded product to remain tough under the sun for as long as possible. This short article will provide moulders with an update on what ‘long term outdoor performance’ really should mean in the 21st century, when you want a polymer that is tough in the sun, for as long as possible. Physical Properties Moulders will usually select a particular grade of polyethylene (PE) that has the necessary physical properties to fulfill the requirements of the moulded part. These properties may include stiffness, impact strength, stress crack resistance, and sintering performance.
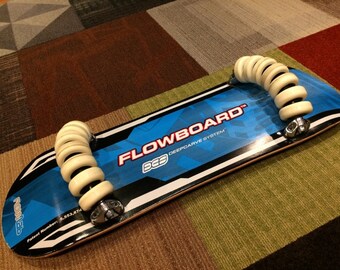
Perhaps the moulder will also undertake some short term evaluation of the moulded part in the field. After you are satisfied that the raw materials and the moulded product are fit for purpose, how do you retain the initial physical properties for as long as possible? Figure 2: 20th century UV Ratings UV and AO Stabilisers Excellent initial physical performance is of no value, unless the product is tough enough to maintain its long term performance under the sun. PE breaks down (degrades) when it is exposed to UV (Ultraviolet) radiation from the sun. Refer to Figure 1. Chemicals called UV stabilizers can be added to polyethylene to significantly reduce the rate of degradation.
The type and level of UV stabilization, as well as its geographical location, will affect the outdoor lifespan of a polyethylene moulding. The level of UV radiation a location receives is measured in KiloLangleys (Kly)1. Typical annual values are 80-120 in Europe, 120-160 in USA, 160-180 in India, and 160-180 in Australia.
You should contact your supplier to confirm the values for your geographic area. Manufacturers of PE incorporate two critical additives: UltraViolet (UV) light stabilisers and AntiOxidant (AO) thermal stabilisers. When raw material suppliers use the words ‘long term’, they are usually referring to long term UV stability.
However, they also may be referring to long term AO stability. There are many different types of light and thermal stabilisers, offering a bewildering range of performance abilities. We will concentrate on the UV stabiliser that provides light protection to the PE, and for simplicity of this article, ignore the important role of thermal or AO stabilisers.
Figure 3: 21st century UV Ratings UV Ratings Moulders generally assess the long- term performance of their PE by referring to the raw material suppliers Technical Data Sheet (TDS). Most suppliers will include a statement on the materials UV characteristics in the TDS. Within the rotomoulding industry we typically use a UV rating system to measure performance.
The most quoted UV rating offered around the world has been UV8. Be aware that some suppliers refuse to provide any UV rating information. Often their TDS’s will simply state that the PE contains UV stabilisers. Moulders considering PE without a UV rating must ask for the UV rating, and it is recommended that you obtain this in writing, as this minimises the risk of misunderstandings. A simple summary of the options typically offered to moulders in the 20th century would have been; (Fig 2) UV0 (no UV protection) UV4 (short term UV protection) UV8 (long term UV protection) When suppliers offered PE with a UV8 rating, they would typically characterise it as ‘long term’ protection. Many moulders have incorrectly assumed that UV8 was the ‘longest term’ UV protection that could be achieved by PE, and still retain Food Contact and Drinking Water approvals.
While this may have been the case in the 20th century, technological advances over the decades has meant that in the 21st century PE can easily achieve UV ratings double and triple the old UV8 standard. UV8 should no longer be thought of as providing ‘long term’ UV protection. Accelerated UV Testing – Natural PE PE weathering tests are generally performed on natural resin with the understanding that with the addition of a pigment, the service life of the product will be enhanced. In order to assess the efficacy of UV additives, an international test method has been established whereby the test sample is subjected to controlled amounts of UV radiation, under controlled temperature and humidity conditions2. It is not really practical for a moulder to undertake weathering tests on the moulded product, so there is a heavy reliance on the artificial accelerated testing to provide guidance on the UV protection the polyethylene may offer.
This is particularly important when moulders are assessing alternative PE grades, manufactured by different suppliers. The two most commonly used methods are ASTM D2565 and ISO 4892-2. They differ significantly in the intensity used – something to be aware of when comparing data. There is an agreed method to compare the two different results. Moulders should always ask for clarification if the test method is not clearly identified. In this article we will be referring to UV ratings in terms of ASTM D2565, which uses an intensity of 0.35W/m2. While the weatherometer test does not yet allow accurate predictions of how a polymer will necessarily behave in the field, it does eliminate the variables associated with differences in climatic conditions and atmospheric pollution and accelerates the availability of performance results.
While the tests are accelerated, testing to UV20 standard (20,000hours) will still take almost 2 years to complete. Generally, 2,000hours corresponds to 1 year in Florida, so 20,000hours is approximately 10 years in Florida.
UV24 Toughest in the sun Within the last 10 years suppliers have begun to respond to industry demands for longer UV testing, and have begun raising the bar on what ‘long term’ stability means. One of the first suppliers in the world to offer moulders superior and longer term UV ratings was Australasian powder manufacturer, ICO Courtenay, (now A.Schulman) when in 2004 they began offering a tank grade with a UV20 rating. The challenge was taken up by the sole Australian producer of rotomoulding PE, Qenos, who in 2008 announced the release of their tank grade with a UV24 rating – as standard.
In 2011 ChevronPhillips and ExxonMobil announced their tank grades had changed from UV8 to UV16 and UV 15 respectively. Moulders should note that these longer term UV ratings are offered by PE producers at no price premium over the old UV8. All these longer term UV options retain Food Contact and Drinking Water approvals. Some of the options now being offered to the rotational moulding industry are; (Fig 3) UV0 (no UV protection) UV8 (‘long’ term protection) UV16 (‘longer’ term protection) UV24 (exceptional protection) Melt Compounding Pigments – for Smarter UV Ratings The quality advantages of melt compounding pigments versus dry blending pigments is well known within the rotomoulding industry. There is an additional cost to the melt compounding process, and in return the quality of the coloured PE powder is significantly better.
Any reader of Rotoworld® over the years will have seen articles on the advantages of melt compounding, and anyone attending rotomoulding conferences around the world will have seen presentations reiterating these advantages. Within Australasia the rotomoulding water and chemical tank industry exclusively use colours that have been melt compounded. There is no dry blending or liquid blending of powders. All the previous references to UV ratings in this article have referred to the light stability of Natural un-pigmented PE.
Guilda Masterbatch Flowboard Magazine Subscription
This is the industry norm, reflecting the prohibitive cost of undertaking any accelerated weathering test of different coloured PE. In Australia there are over 20 different colour shades used by the tank industry, which comply with the minimum UV rating prescribed by the Australasian tank standard – AS/NZS4766. This UV rating is based on the natural polyethylene. Accelerated UV Testing – Pigmented PE An Australian colour masterbatch company, Guilda Pty Ltd, commissioned a long term UV weatherometer testing program to be undertaken on four of the most popular tank colours in Australasia. Guilda supply colour masterbatches to Australasian and Asian compounders. The accelerated artificial weathering test was undertaken using ISO4892 test method, which subjects the samples to an intensity of 0.51/W/m2.
As mentioned in a previous paragraph this intensity is different to ASTM D2565. The testing company has adjusted the 0.51/W/m2 results to 0.35W/m2 exposure so that we are consistent in our use of UV ratings. All four colours tested were in the same grade of polyethylene, with the same light stabilisation and the same thermal stabilisation.
Guilda Masterbatch Flowboard Magazines
Only the pigments were different. After 36,000hours, or just over 4 years of accelerated testing, all four colours easily retained greater than 50% of their original break elongation. Industry convention defines the end of the UV test when there is a 50% decline in original break elongation. UV36 Rating – Pigmented PE All four melt compounded colours achieved a UV rating of UV36. Python pyenv. 36,000hrs is approximately 18 years exposure in Florida (@ 660 Kly/Yr), or 15 years in Arizona, Australia and India (@ 750 Kly/Yr). It is very encouraging to know that despite the cost and time involved, a relatively small family-owned raw material supplier is willing to undertake a 4 year testing project to verify that their melt compounded colour formulations provide moulders with exceptional long term and very smart UV protection.
Superior UV Performance – Strength and Integrity If you want to achieve ‘long term outdoor performance’ for your moulded products, one of the critical raw material properties you should review right now is the UV. The UV8 rating no longer defines a raw material as having ‘long term’ protection.
UV15 and UV16 ratings are now the new standard for longer term protection in North American, while in Australia a UV24 rating is the standard for exceptional longer term protection. If you are looking for polyethylene that is truly tough in the sun, you really need UV15 as the minimum. If your PE has not changed from UV8 to at least UV15, ask your supplier why they have not.
It can be achieved without any extra cost. Australia is leading the world in providing moulders with materials that really have seriously long term UV ratings, with UV24 polyethylene being the standard for the past 5 years. Make sure your suppliers know that you are aware that UV performance ‘for as long as possible’ can be measured today with a UV24 rating. References 1 & 2 ARMA Materials Properties Testing Guide V4.